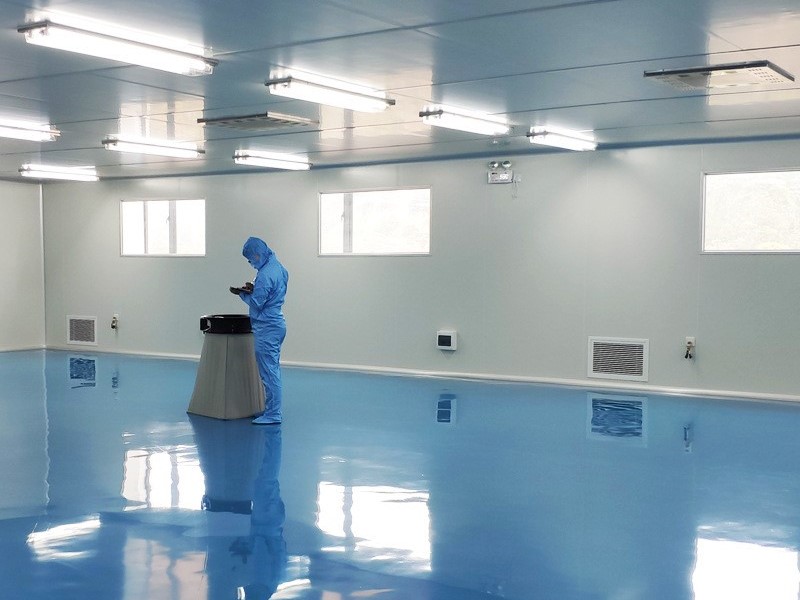
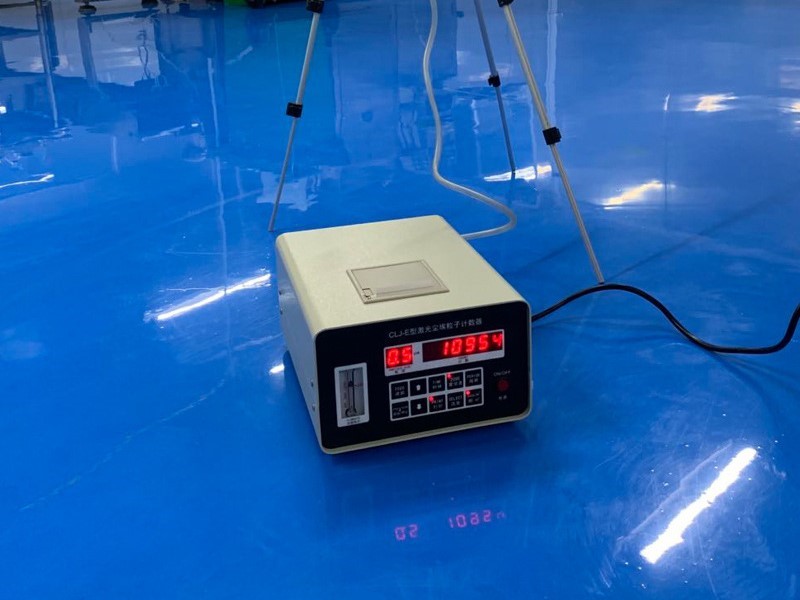
வகுப்பு 10000 தரநிலையுடன் ஆன்-சைட் கமிஷனுக்குப் பிறகு, காற்றின் அளவு (காற்று மாற்றங்களின் எண்ணிக்கை), அழுத்த வேறுபாடு மற்றும் வண்டல் பாக்டீரியா போன்ற அளவுருக்கள் அனைத்தும் வடிவமைப்பு (GMP) தேவைகளைப் பூர்த்தி செய்கின்றன, மேலும் தூசி துகள் கண்டறிதலின் ஒரே ஒரு உருப்படி மட்டுமே தகுதியற்றது. (வகுப்பு 100000).பெரிய துகள்கள், முக்கியமாக 5 μm மற்றும் 10 μm துகள்கள் தரத்தை மீறுவதாக எதிர் அளவீட்டு முடிவுகள் காட்டுகின்றன.
1. தோல்வி பகுப்பாய்வு
பெரிய துகள்கள் தரத்தை மீறுவதற்கான காரணம் பொதுவாக அதிக தூய்மையான துப்புரவு அறைகளில் ஏற்படுகிறது.சுத்தம் அறையின் சுத்திகரிப்பு விளைவு நன்றாக இல்லை என்றால், அது நேரடியாக சோதனை முடிவுகளை பாதிக்கும்;காற்றின் அளவு தரவு மற்றும் முந்தைய பொறியியல் அனுபவத்தின் பகுப்பாய்வு மூலம், சில அறைகளின் தத்துவார்த்த சோதனை முடிவுகள் 1000 வகுப்பாக இருக்க வேண்டும்;ஆரம்ப பகுப்பாய்வு பின்வருமாறு அறிமுகப்படுத்தப்பட்டது:
①துப்புரவு பணி தரமானதாக இல்லை.
②.ஹெபா வடிகட்டியின் சட்டத்தில் இருந்து காற்று கசிவு உள்ளது.
③.ஹெபா வடிகட்டியில் கசிவு உள்ளது.
④சுத்தம் அறையில் எதிர்மறை அழுத்தம்.
⑤.காற்றின் அளவு போதுமானதாக இல்லை.
⑥.ஏர் கண்டிஷனிங் யூனிட்டின் வடிகட்டி அடைக்கப்பட்டுள்ளது.
⑦.புதிய காற்று வடிகட்டி தடுக்கப்பட்டுள்ளது.
மேற்கூறிய பகுப்பாய்வின் அடிப்படையில், சுத்தம் அறையின் நிலையை மறு-சோதனை செய்ய பணியாளர்களை அமைப்பு ஏற்பாடு செய்தது மற்றும் வடிவமைப்புத் தேவைகளைப் பூர்த்தி செய்ய காற்றின் அளவு, அழுத்தம் வேறுபாடு போன்றவற்றைக் கண்டறிந்தது.அனைத்து சுத்தமான அறைகளின் தூய்மை 100000 வகுப்பு மற்றும் 5 μm மற்றும் 10 μm தூசி துகள்கள் தரத்தை மீறியது மற்றும் வகுப்பின் 10000 வடிவமைப்பு தேவைகளை பூர்த்தி செய்யவில்லை.
2. சாத்தியமான தவறுகளை ஒவ்வொன்றாக பகுப்பாய்வு செய்து அகற்றவும்
முந்தைய திட்டங்களில், புதிய காற்று வடிகட்டி அல்லது யூனிட்டில் முதன்மை அல்லது நடுத்தர செயல்திறன் அடைப்பு காரணமாக போதுமான அழுத்த வேறுபாடு மற்றும் குறைந்த காற்று விநியோக அளவு ஏற்படும் சூழ்நிலைகள் உள்ளன.யூனிட்டைப் பரிசோதித்து, அறையில் காற்றின் அளவை அளவிடுவதன் மூலம், உருப்படிகள் ④⑤⑥⑦ உண்மை இல்லை என்று தீர்மானிக்கப்பட்டது;மீதமுள்ள அடுத்தது உட்புற தூய்மை மற்றும் செயல்திறன் பற்றிய பிரச்சினை;உண்மையில் தளத்தில் சுத்தம் செய்யப்படவில்லை.சிக்கலை ஆய்வு செய்து பகுப்பாய்வு செய்யும் போது, தொழிலாளர்கள் ஒரு சுத்தமான அறையை சிறப்பாக சுத்தம் செய்திருந்தனர்.அளவீட்டு முடிவுகள் இன்னும் பெரிய துகள்கள் தரத்தை மீறுவதாகக் காட்டியது, பின்னர் ஸ்கேன் மற்றும் வடிகட்ட ஹெப்பா பெட்டியை ஒவ்வொன்றாகத் திறந்தது.ஸ்கேன் முடிவுகள், ஒரு ஹெப்பா வடிகட்டி நடுவில் சேதமடைந்துள்ளதாகவும், மற்ற அனைத்து வடிப்பான்கள் மற்றும் ஹெபா பாக்ஸுக்கு இடையே உள்ள சட்டகத்தின் துகள் எண்ணிக்கை அளவீட்டு மதிப்புகள் திடீரென்று அதிகரித்தன, குறிப்பாக 5 μm மற்றும் 10 μm துகள்களுக்கு.
3. தீர்வு
பிரச்சனைக்கான காரணம் கண்டுபிடிக்கப்பட்டதால், அதைத் தீர்ப்பது எளிது.இந்த திட்டத்தில் பயன்படுத்தப்படும் ஹெபா பாக்ஸ் அனைத்தும் போல்ட் அழுத்தப்பட்ட மற்றும் பூட்டப்பட்ட வடிகட்டி கட்டமைப்புகள் ஆகும்.வடிகட்டி சட்டத்திற்கும் ஹெப்பா பெட்டியின் உள் சுவருக்கும் இடையே 1-2 செ.மீ இடைவெளி உள்ளது.சீல் கீற்றுகள் மூலம் இடைவெளிகளை நிரப்பி, நடுநிலை முத்திரை குத்த பயன்படும் மெழுகு போன்ற ஒரு வகை சீல் மூலம் அவற்றை அடைத்த பிறகு, அறையின் தூய்மை இன்னும் 100000 வகுப்பில் உள்ளது.
4. தவறு மறு பகுப்பாய்வு
இப்போது ஹெபா பாக்ஸின் சட்டகம் சீல் செய்யப்பட்டு, வடிகட்டி ஸ்கேன் செய்யப்பட்டதால், வடிகட்டியில் கசிவு புள்ளி இல்லை, எனவே காற்று வென்ட்டின் உள் சுவரின் சட்டத்தில் சிக்கல் இன்னும் ஏற்படுகிறது.பின்னர் சட்டத்தை மீண்டும் ஸ்கேன் செய்தோம்: ஹெப்பா பெட்டியின் உள் சுவர் சட்டத்தின் கண்டறிதல் முடிவுகள்.முத்திரையை கடந்து சென்ற பிறகு, ஹெபா பெட்டியின் உள் சுவரின் இடைவெளியை மீண்டும் பரிசோதித்து, பெரிய துகள்கள் இன்னும் தரத்தை மீறுவதைக் கண்டறிந்தது.முதலில், வடிகட்டி மற்றும் உள் சுவருக்கு இடையே உள்ள கோணத்தில் சுழல் மின்னோட்டம் என்று நாங்கள் நினைத்தோம்.ஹெப்பா ஃபில்டர் ஃப்ரேமில் 1மீ ஃபிலிம் தொங்கவிடத் தயார் செய்தோம்.இடது மற்றும் வலது படங்கள் ஒரு கேடயமாக பயன்படுத்தப்படுகின்றன, பின்னர் ஹெபா வடிகட்டியின் கீழ் தூய்மை சோதனை மேற்கொள்ளப்படுகிறது.படத்தை ஒட்டுவதற்குத் தயாராகும் போது, உள் சுவரில் பெயிண்ட் உரித்தல் நிகழ்வு இருப்பதும், உள் சுவரில் முழு இடைவெளியும் இருப்பதும் கண்டறியப்பட்டது.
5. ஹெப்பா பெட்டியில் இருந்து தூசியை கையாளவும்
ஹெப்பா பாக்ஸின் உள் சுவரில் அலுமினிய ஃபாயில் டேப்பை ஒட்டவும், ஏர் போர்ட்டின் உள் சுவரில் உள்ள தூசியை குறைக்கவும்.அலுமினிய ஃபாயில் டேப்பை ஒட்டிய பிறகு, ஹெப்பா ஃபில்டர் ஃப்ரேமில் உள்ள தூசித் துகள்களின் எண்ணிக்கையைக் கண்டறியவும்.பிரேம் கண்டறிதலைச் செயலாக்கிய பிறகு, செயலாக்கத்திற்கு முன்னும் பின்னும் துகள் எதிர் கண்டறிதல் முடிவுகளை ஒப்பிடுவதன் மூலம், தரத்தை மீறும் பெரிய துகள்களுக்கான காரணம் ஹெபா பாக்ஸால் சிதறடிக்கப்பட்ட தூசியால் ஏற்படுகிறது என்பதை தெளிவாக தீர்மானிக்க முடியும்.டிஃப்பியூசர் அட்டையை நிறுவிய பின், சுத்தமான அறை மீண்டும் சோதிக்கப்பட்டது.
6. சுருக்கம்
க்ளீன்ரூம் திட்டத்தில் தரத்தை மீறும் பெரிய துகள் அரிதானது, மேலும் அதை முற்றிலும் தவிர்க்கலாம்;இந்த துப்புரவுத் திட்டத்தில் உள்ள சிக்கல்களின் சுருக்கம் மூலம், திட்ட மேலாண்மை எதிர்காலத்தில் பலப்படுத்தப்பட வேண்டும்;மூலப்பொருள் கொள்முதலின் தளர்வான கட்டுப்பாடு காரணமாக இந்தப் பிரச்சனை ஏற்படுகிறது, இது ஹெப்பா பெட்டியில் சிதறிய தூசிக்கு வழிவகுக்கிறது.கூடுதலாக, நிறுவல் செயல்பாட்டின் போது ஹெபா பாக்ஸ் அல்லது பெயிண்ட் உரித்தல் ஆகியவற்றில் எந்த இடைவெளிகளும் இல்லை.கூடுதலாக, வடிகட்டி நிறுவப்படுவதற்கு முன்பு எந்த காட்சி ஆய்வும் இல்லை, மேலும் வடிகட்டி நிறுவப்பட்ட போது சில போல்ட்கள் இறுக்கமாக பூட்டப்படவில்லை, இவை அனைத்தும் நிர்வாகத்தில் பலவீனங்களைக் காட்டின.ஹெபா பாக்ஸில் இருந்து வரும் தூசிதான் முக்கிய காரணம் என்றாலும், சுத்தமான அறையின் கட்டுமானம் தொய்வாக இருக்க முடியாது.கட்டுமானத்தின் தொடக்கத்திலிருந்து முடிவடையும் வரை செயல்முறை முழுவதும் தர மேலாண்மை மற்றும் கட்டுப்பாட்டை மேற்கொள்வதன் மூலம் மட்டுமே எதிர்பார்க்கப்படும் முடிவுகளை ஆணையிடும் கட்டத்தில் அடைய முடியும்.
இடுகை நேரம்: செப்-01-2023