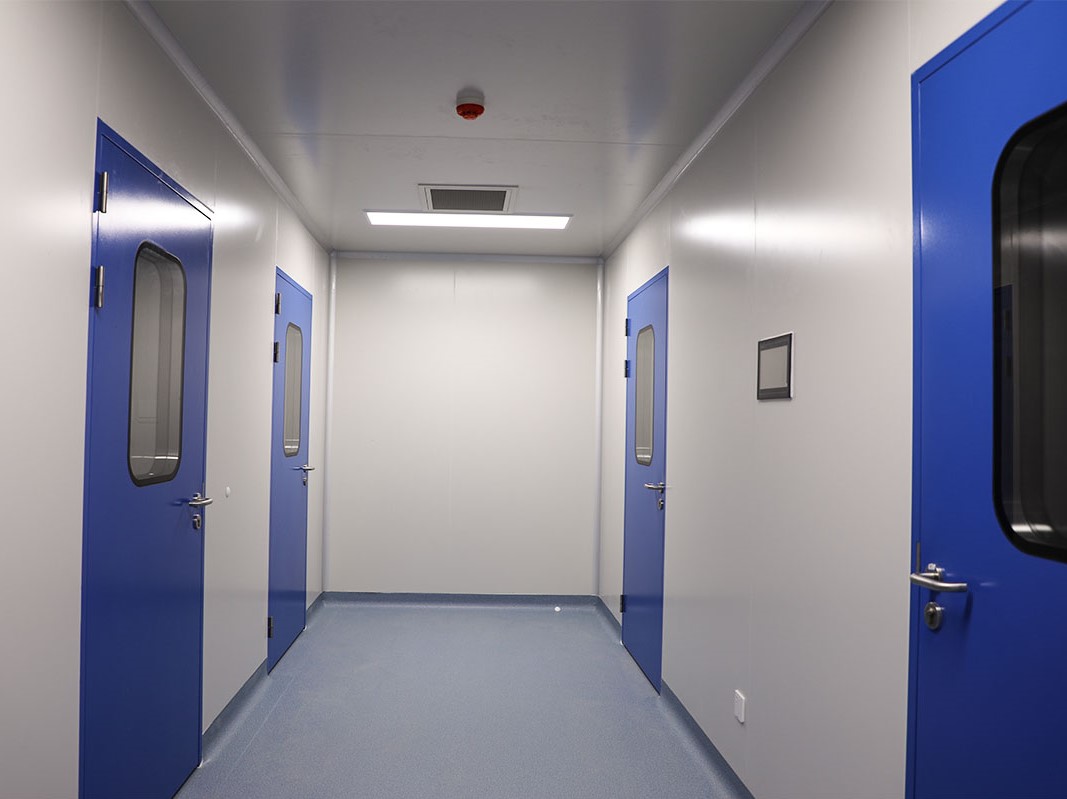
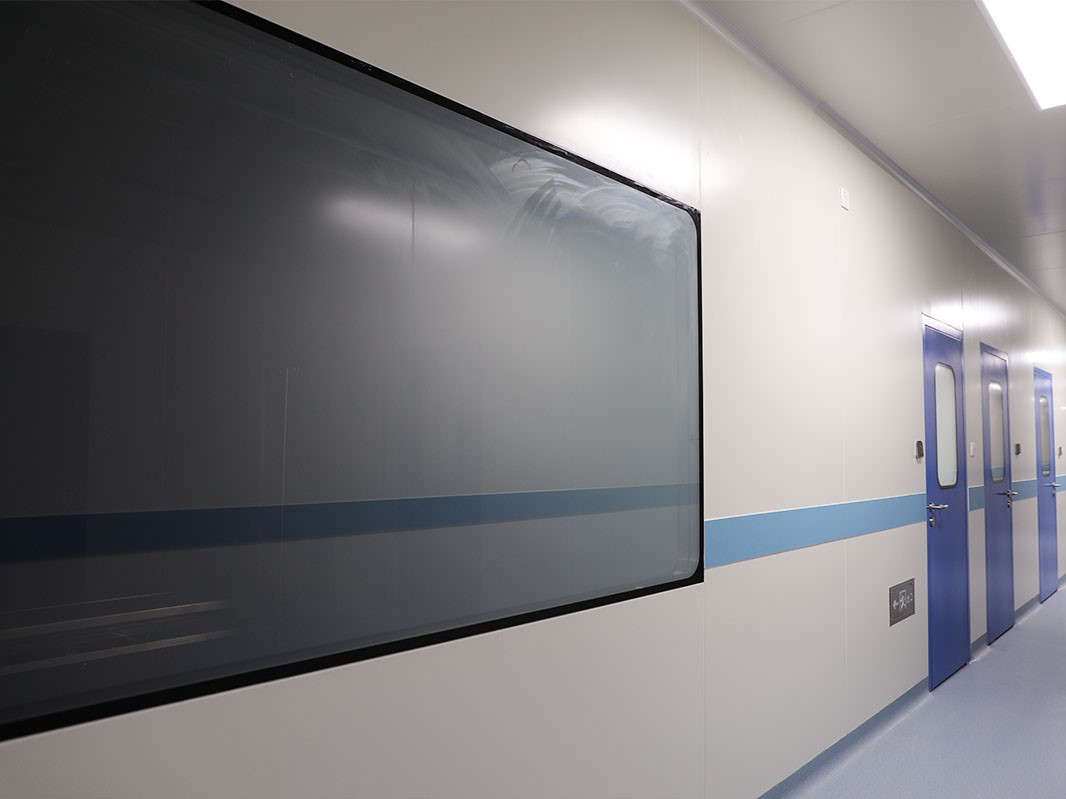
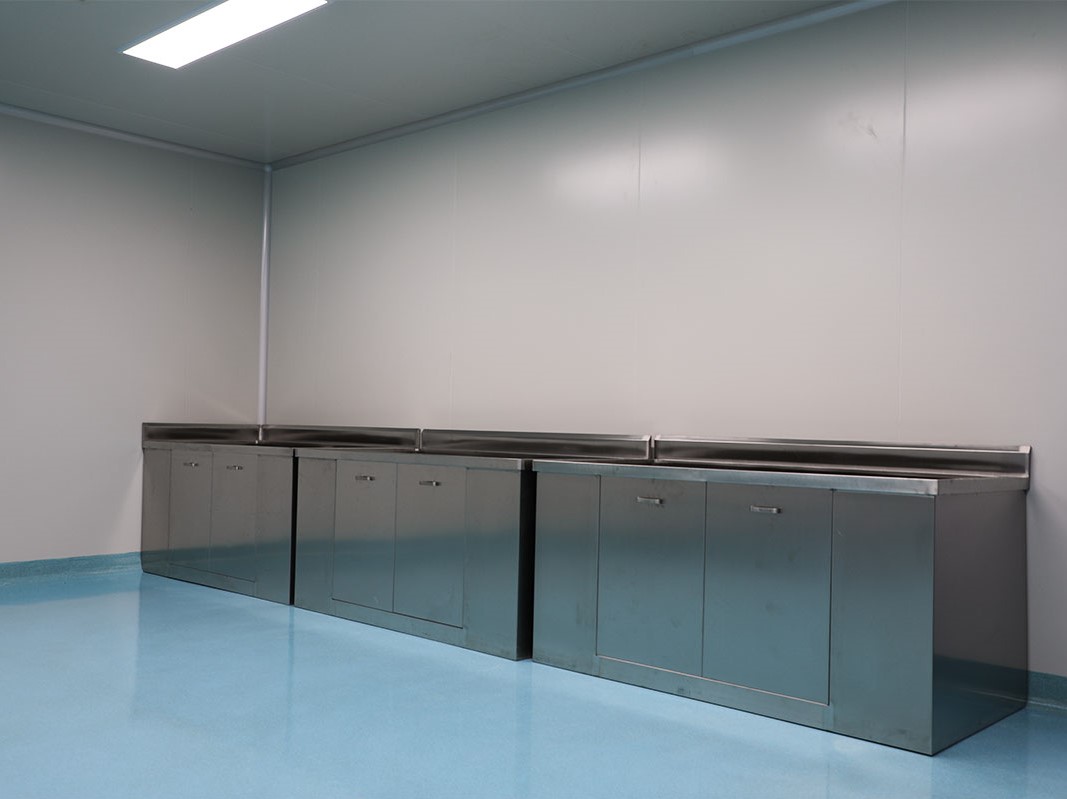
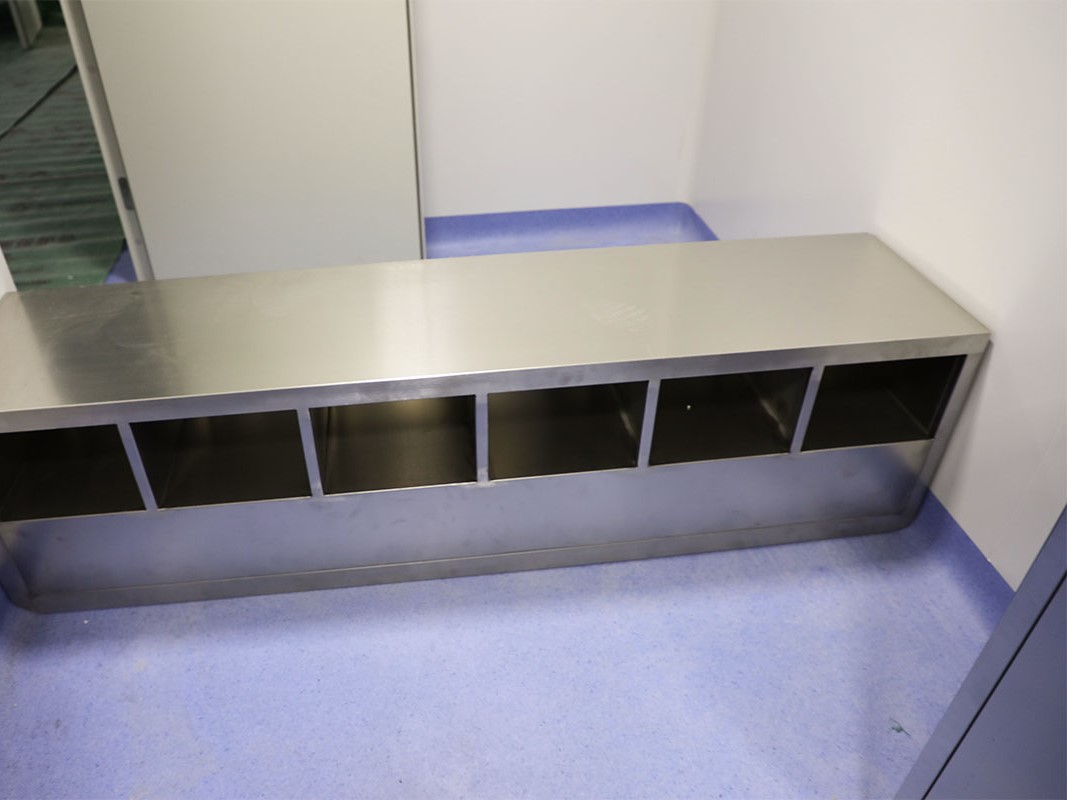
1992 இல் வெளியிடப்பட்டதிலிருந்து, சீனாவின் மருந்துத் துறையில் "மருந்துகளுக்கான நல்ல உற்பத்தி நடைமுறை" (GMP) படிப்படியாக மருந்து உற்பத்தி நிறுவனங்களால் அங்கீகரிக்கப்பட்டு, ஏற்றுக்கொள்ளப்பட்டு, செயல்படுத்தப்பட்டு வருகிறது.GMP என்பது நிறுவனங்களுக்கான தேசிய கட்டாயக் கொள்கையாகும், மேலும் குறிப்பிட்ட கால வரம்பிற்குள் தேவைகளைப் பூர்த்தி செய்யத் தவறிய நிறுவனங்கள் உற்பத்தியை நிறுத்திவிடும்.
GMP சான்றிதழின் முக்கிய உள்ளடக்கம் மருந்து உற்பத்தியின் தர மேலாண்மை கட்டுப்பாடு ஆகும்.அதன் உள்ளடக்கத்தை இரண்டு பகுதிகளாகப் பிரிக்கலாம்: மென்பொருள் மேலாண்மை மற்றும் வன்பொருள் வசதிகள்.சுத்தமான அறை கட்டிடம் வன்பொருள் வசதிகளில் முக்கிய முதலீட்டு கூறுகளில் ஒன்றாகும்.சுத்தமான அறை கட்டிடம் முடிந்த பிறகு, அது வடிவமைப்பு நோக்கங்களை அடைய முடியுமா மற்றும் GMP தேவைகளை பூர்த்தி செய்ய முடியுமா என்பது இறுதியில் சோதனை மூலம் உறுதிப்படுத்தப்பட வேண்டும்.
சுத்தமான அறையின் ஆய்வின் போது, அவர்களில் சிலர் தூய்மைப் பரிசோதனையில் தோல்வியடைந்தனர், சிலர் தொழிற்சாலைக்கு உள்ளூர் மற்றும் சிலர் முழுத் திட்டமாக இருந்தனர்.சரிபார்ப்பு, பிழைத்திருத்தம், சுத்தம் செய்தல் போன்றவற்றின் மூலம் இரு தரப்பினரும் தேவைகளை அடைந்திருந்தாலும், ஆய்வு தகுதியற்றதாக இருந்தால், அது பெரும்பாலும் மனிதவளம் மற்றும் பொருள் வளங்களை நிறைய வீணாக்குகிறது, கட்டுமான காலத்தை தாமதப்படுத்துகிறது மற்றும் GMP சான்றிதழின் செயல்முறையை தாமதப்படுத்துகிறது.சோதனைக்கு முன் சில காரணங்கள் மற்றும் குறைபாடுகள் தவிர்க்கப்படலாம்.எங்கள் உண்மையான வேலையில், தகுதியற்ற தூய்மை மற்றும் GMP தோல்விக்கான முக்கிய காரணங்கள் மற்றும் முன்னேற்ற நடவடிக்கைகளில் பின்வருவன அடங்கும்:
1. நியாயமற்ற பொறியியல் வடிவமைப்பு
இந்த நிகழ்வு ஒப்பீட்டளவில் அரிதானது, முக்கியமாக குறைந்த தூய்மை தேவைகள் கொண்ட சிறிய சுத்தமான அறைகளை நிர்மாணிப்பதில்.சுத்தமான அறை பொறியியலில் போட்டி இப்போது ஒப்பீட்டளவில் கடுமையாக உள்ளது, மேலும் சில கட்டுமானப் பிரிவுகள் திட்டத்தைப் பெறுவதற்கான ஏலத்தில் குறைந்த மேற்கோள்களை வழங்கியுள்ளன.கட்டுமானத்தின் பிற்பகுதியில், சில அலகுகள் மூலைகளை வெட்டவும், குறைந்த ஆற்றல் கொண்ட ஏர் கண்டிஷனிங் மற்றும் காற்றோட்ட அமுக்கி அலகுகளைப் பயன்படுத்தவும் பயன்படுத்தப்பட்டன.மற்றொரு காரணம், வடிவமைப்பு மற்றும் கட்டுமானத் தொடக்கத்திற்குப் பிறகு பயனர் புதிய தேவைகள் மற்றும் சுத்தமான பகுதியைச் சேர்த்துள்ளார், இது அசல் வடிவமைப்பையும் தேவைகளைப் பூர்த்தி செய்ய முடியாமல் போகும்.இந்த பிறவி குறைபாடு மேம்படுத்த கடினமாக உள்ளது மற்றும் பொறியியல் வடிவமைப்பு கட்டத்தில் தவிர்க்கப்பட வேண்டும்.
2. உயர்தர தயாரிப்புகளை குறைந்த விலை தயாரிப்புகளுடன் மாற்றுதல்
சுத்தமான அறைகளில் ஹெப்பா ஃபில்டர்களைப் பயன்படுத்துவதில், 100000 அல்லது அதற்கு மேற்பட்ட தூய்மை நிலையுடன் காற்று சுத்திகரிப்பு சிகிச்சைக்கு, முதன்மை, நடுத்தர மற்றும் ஹெபா வடிகட்டிகளின் மூன்று-நிலை வடிகட்டுதல்களைப் பயன்படுத்த வேண்டும் என்று நாடு விதிக்கிறது.சரிபார்ப்பு செயல்பாட்டின் போது, ஒரு பெரிய சுத்தமான அறை திட்டமானது ஹெபா காற்று வடிகட்டியை 10000 தூய்மையான அளவில் மாற்றுவதற்கு சப் ஹெபா ஏர் ஃபில்டரைப் பயன்படுத்தியது, இதன் விளைவாக தகுதியற்ற தூய்மை ஏற்பட்டது.இறுதியாக, GMP சான்றிதழின் தேவைகளைப் பூர்த்தி செய்ய உயர் திறன் வடிகட்டி மாற்றப்பட்டது.
3. காற்று விநியோக குழாய் அல்லது வடிகட்டியின் மோசமான சீல்
இந்த நிகழ்வு கரடுமுரடான கட்டுமானத்தால் ஏற்படுகிறது, ஏற்றுக்கொள்ளும் போது, ஒரு குறிப்பிட்ட அறை அல்லது அதே அமைப்பின் ஒரு பகுதி தகுதியற்றது என்று தோன்றலாம்.காற்று விநியோகக் குழாயின் கசிவு சோதனை முறையைப் பயன்படுத்துவது மேம்படுத்தல் முறையாகும், மேலும் வடிகட்டியின் குறுக்குவெட்டு, சீல் பசை மற்றும் நிறுவல் சட்டத்தை ஸ்கேன் செய்ய, கசிவு இடத்தைக் கண்டறிந்து, கவனமாக சீல் செய்ய ஒரு துகள் கவுண்டரைப் பயன்படுத்துகிறது.
4. திரும்பும் காற்று குழாய்கள் அல்லது காற்று துவாரங்களின் மோசமான வடிவமைப்பு மற்றும் ஆணையிடுதல்
வடிவமைப்பு காரணங்களின் அடிப்படையில், சில நேரங்களில் இட வரம்புகள் காரணமாக, "டாப் சப்ளை சைட் ரிட்டர்ன்" அல்லது போதுமான எண்ணிக்கையிலான ரிட்டர்ன் ஏர் வென்ட்களைப் பயன்படுத்துவது சாத்தியமில்லை.வடிவமைப்பு காரணங்களை நீக்கிய பிறகு, திரும்பும் காற்று துவாரங்களின் பிழைத்திருத்தமும் ஒரு முக்கியமான கட்டுமான இணைப்பாகும்.பிழைத்திருத்தம் சரியாக இல்லாவிட்டால், திரும்பும் காற்று வெளியின் எதிர்ப்பானது மிக அதிகமாகவும், திரும்பும் காற்றின் அளவு விநியோக காற்றின் அளவை விட குறைவாகவும் இருந்தால், அது தகுதியற்ற தூய்மையையும் ஏற்படுத்தும்.கூடுதலாக, கட்டுமானத்தின் போது தரையில் இருந்து திரும்பும் காற்று வெளியீட்டின் உயரமும் தூய்மையை பாதிக்கிறது.
5. சோதனையின் போது சுத்தமான அறை அமைப்புக்கு போதுமான சுய சுத்திகரிப்பு நேரம் இல்லை
தேசிய தரத்தின்படி, சுத்திகரிப்பு ஏர் கண்டிஷனிங் அமைப்பு சாதாரணமாக இயங்கிய 30 நிமிடங்களுக்குப் பிறகு சோதனை முயற்சி தொடங்கப்படும்.இயங்கும் நேரம் மிகக் குறைவாக இருந்தால், அது தகுதியற்ற தூய்மையையும் ஏற்படுத்தும்.இந்த வழக்கில், ஏர் கண்டிஷனிங் சுத்திகரிப்பு அமைப்பின் இயக்க நேரத்தை சரியான முறையில் நீட்டிக்க போதுமானது.
6. சுத்திகரிப்பு ஏர் கண்டிஷனிங் அமைப்பு முழுமையாக சுத்தம் செய்யப்படவில்லை
கட்டுமானச் செயல்பாட்டின் போது, முழு சுத்திகரிப்பு ஏர் கண்டிஷனிங் அமைப்பு, குறிப்பாக விநியோக மற்றும் திரும்பும் காற்று குழாய்கள், ஒரே நேரத்தில் முடிக்கப்படவில்லை, மேலும் கட்டுமான பணியாளர்கள் மற்றும் கட்டுமான சூழல் காற்றோட்ட குழாய்கள் மற்றும் வடிகட்டிகளுக்கு மாசுபாட்டை ஏற்படுத்தும்.முழுமையாக சுத்தம் செய்யாவிட்டால், அது நேரடியாக சோதனை முடிவுகளை பாதிக்கும்.கட்டுமானத்தின் போது சுத்தம் செய்வதே முன்னேற்ற நடவடிக்கையாகும், மேலும் பைப்லைன் நிறுவலின் முந்தைய பகுதியை நன்கு சுத்தம் செய்த பிறகு, சுற்றுச்சூழல் காரணிகளால் ஏற்படும் மாசுபாட்டைத் தவிர்க்க பிளாஸ்டிக் படலத்தை மூடுவதற்கு பயன்படுத்தலாம்.
7. சுத்தமான பட்டறை முழுமையாக சுத்தம் செய்யப்படவில்லை
சந்தேகத்திற்கு இடமின்றி, சோதனை தொடரும் முன் ஒரு சுத்தமான பட்டறை நன்கு சுத்தம் செய்யப்பட வேண்டும்.துப்புரவு பணியாளர்களின் மனித உடலால் ஏற்படும் மாசுபாட்டை அகற்ற, சுத்தம் செய்வதற்கு இறுதி துடைக்கும் பணியாளர்கள் சுத்தமான பணி ஆடைகளை அணிய வேண்டும்.துப்புரவு முகவர்கள் குழாய் நீர், தூய நீர், ஆர்கானிக் கரைப்பான்கள், நடுநிலை சவர்க்காரம் போன்றவையாக இருக்கலாம். நிலையான எதிர்ப்புத் தேவைகள் உள்ளவர்கள், நிலையான எதிர்ப்பு திரவத்தில் தோய்த்த துணியால் நன்கு துடைக்கவும்.
இடுகை நேரம்: ஜூலை-26-2023